Interested Article - Углепластики
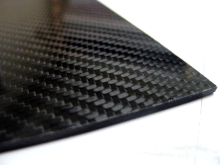
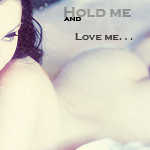
- 2021-10-11
- 1
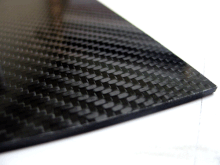

Карбон ( углепластики , карбонопластики , от англ. carbon — углерод) — полимерные композитные материалы из переплетённых нитей углеродного волокна , расположенных в матрице из полимерных (например, эпоксидных ) смол. Плотность — от 1450 кг/м³ до 2000 кг/м³.
Материалы отличаются высокой прочностью, жёсткостью и малой массой, часто прочнее стали , и гораздо легче. По удельным характеристикам превосходит высокопрочную сталь, например, легированную конструкционную сталь 25ХГСА.
Вследствие дороговизны, при экономии средств и отсутствии необходимости получения максимальных характеристик этот материал применяют в качестве усиливающих дополнений в основном материале конструкции.
Основные сведения
Основная составляющая часть углепластика — это нити углеродного волокна , состоящего в основном из атомов углерода . Такие нити очень тонкие (примерно 0,005-0,010 мм в диаметре ), сломать их очень просто, а вот порвать достаточно трудно. Из этих нитей сплетаются ткани. Они могут иметь разный рисунок плетения (ёлочка, рогожа и др.).
Для придания ещё большей прочности ткани, нити углерода кладут слоями, каждый раз меняя угол направления плетения. Слои скрепляются с помощью эпоксидных смол .
Нити углерода обычно получают термической обработкой химических или природных органических волокон, при которой в материале волокна остаются главным образом атомы углерода. Термическая обработка состоит из нескольких этапов:
- Первый из них представляет собой окисление исходного ( полиакрилонитрильного , вискозного ) волокна на воздухе при температуре 250 °C в течение 24 часов. В результате окисления образуются лестничные структуры.
- После окисления следует стадия карбонизации — нагрева волокна в среде азота или аргона при температурах от 800 до 1500 °C. В результате карбонизации происходит образование графитоподобных структур.
- Процесс термической обработки заканчивается графитизацией при температуре 1600-3000 °C, которая также проходит в инертной среде. В результате графитизации количество углерода в волокне доводится до 99 %.
Помимо обычных органических волокон (чаще всего вискозных и полиакрилонитрильных), для получения нитей углерода могут быть использованы специальные волокна из фенольных смол, лигнина , каменноугольных и нефтяных пеков . Кроме того, детали из карбона превосходят по прочности детали из стекловолокна , но, при этом, обходятся значительно дороже.
Дороговизна карбона вызвана, прежде всего, более сложной технологией производства и большей стоимостью производных материалов. Например, для проклейки слоёв используются более дорогие и качественные смолы, чем при работе со стеклонитью, а для производства деталей требуется более дорогое оборудование (к примеру, такое как автоклав ).
Недостатки
При производстве углепластиков необходимо очень строго выдерживать технологические параметры, при нарушении которых прочностные свойства изделий резко снижаются. Необходимы сложные и дорогостоящие меры контроля качества изделий (в том числе, ультразвуковая дефектоскопия , рентгеновская, оптическая голография и даже акустический контроль).
Другим серьёзным недостатком углепластиков является их низкая стойкость по отношению к ударным нагрузкам . Повреждения конструкций при ударах посторонними предметами (даже при падении инструмента на неё) в виде внутренних трещин и расслоений могут быть невидимы глазу, но приводят к снижению прочности; разрушение повреждённой ударами конструкции может произойти уже при относительной деформации , равной 0,5 % .
Производство

- Прессование . Углеткань выстилается в форму, предварительно смазанную антиадгезивом (например, мыло, воск , воск в бензине, Циатим-221 , кремнийорганические смазки ). Пропитывается смолой. Излишки смолы удаляются в вакууме (вакуум-формование) или под давлением. Смола полимеризуется, иногда при нагревании. После полимеризации смолы изделие готово.
- Контактное формование . На примере изготовления бампера: берётся металлический исходный бампер, смазывается разделительным слоем. Затем на него напыляется монтажная пена ( гипс , алебастр ). После отвердевания снимается. Это матрица. Затем её смазывают разделительным слоем и выкладывают ткань. Ткань может быть предварительно пропитанной, а может пропитываться кистью или поливом непосредственно в матрице. Затем ткань прокатывается валиками — для уплотнения и удаления пузырьков воздуха. Затем полимеризация (если отвердитель горячего отверждения , то в печи, если нет, то при комнатной температуре — 25 °C). Затем бампер снимается, если надо — шлифуется и красится.
- Вакуумная инфузия . На подготовленную матрицу выкладывается углеродная ткань (без пропитки), далее выкладываются технологические слои для равномерного распространения связующего. Под технологический пакет подаётся разрежение. После этого открывается клапан подачи связующего и оно, под действием вакуума заполняет пустоты и пропитывает углеродную ткань.
- Вакуумное формование. Это изменение формы плоских заготовок (листов или плёнок) из термопластичного полимерного материала при повышенных температурах и воздействии вакуума в объёмные формованные изделия. За счёт относительно невысокой стоимости технологической оснастки, данная технология оказывается крайне привлекательной при изготовлении партий изделий от 10 до 5000 шт., а иногда и до 30.000 шт.
- Пултрузия . Технология изготовления высоконаполненных волокном композиционных деталей с постоянной поперечной структурой. В настоящее время активно используется в производстве полимерных композиционных материалов, например, для производства углеродных ламелей (пластин).
- Намотка . Суть технологии заключается в непрерывном наматывании предварительно пропитанного ровинга /ов (стеклянного, углеродного, базальтового, комбинированного) или ленты на предварительно подготовленную форму – мандрель. После намотки необходимого количества слоёв, мандрель с намотанными слоями помещается в нагревательную печь для дальнейшей полимеризации.
- RTM. Сухой армирующий материал укладывается между двух частей герметично закрытой жёсткой оснастки. Связующее низкой вязкости подаётся под давлением в пресс-форму, вытесняя воздух в сторону дренажных каналов до тех пор, пока форма не будет полностью заполнена. Пресс-формы для этой технологии, как правило, изготавливаются из металла с низким КЛТР. Данная технология хорошо подходит для мелкосерийного и серий средних объёмов от 500 до 2 0000 изделий в год.
- LFI . Технология LFI (Long Fiber Injection - длинноволоконная инжекция) была разработана немецкой фирмой Krauss Maffei в 1995 году. Характеристика производства: инжекция длинного волокна, процесс используемый для производства компонентов интерьера и экстерьера автомобилей, конструкция которых имеет сложную форму, крупные габариты и окрашенную поверхность класса А. В этом процессе рубленое волокно из ассемблированного ровинга, напыляется в форму (матрицу) с контролируемой температурой. В это же время смешивается жидкий изоцианат и полиол, подаётся совместно с рубленым волокном в матрицу. Все эти компоненты напыляются в форму (матрицу), форма смыкается и заполняются путём расширения полиуретановой пены в результате химической реакции введённых компонентов. Несколько минут спустя, полимеризация закончена и изделие может быть извлечено из матрицы.
- SMC/BMC. Материал нарезается, в соответствии со схемой раскроя, и переносится в пресс-форму, нагретую до рабочей температуры. Пресс-форма смыкается, в результате чего под давлением материал растекается в полости формы и отверждается. В конце цикла изделие извлекается из пресс-формы, и производится его окончательная механическая обработка и окраска (если это необходимо).
Трубы и иные цилиндрические изделия производят намоткой. Форма волокна: нить, лента, ткань. Смола: эпоксидная или полиэфирная . Возможно изготовление форм из углепластика в домашних условиях, при наличии опыта и оборудования.

Применение
Углепластики широко используются при изготовлении лёгких, но прочных деталей, заменяя собой металлы, во многих изделиях от частей космических кораблей до удочек, среди которых:

- ракетно-космическая техника;
- авиатехника ( самолётостроение , вертолётостроение (например, несущие винты));
- судостроение ( корабли , спортивное судостроение );
- автомобилестроение ( спортивные автомобили (например, бамперы , пороги, двери, крышки капотов), мотоциклы, прототипы MotoGP, болиды Формулы 1 ( кокпиты и обтекатели), а также при оформлении салонов;
- наука и исследования;
- усиление железобетонных конструкций;
- спортивный инвентарь ( роликовые коньки , велосипеды , футбольные бутсы, хоккейные клюшки , сноуборды, лыжи , лыжные палки и ботинки, ракетки для тенниса , основания для настольного тенниса, лезвия коньков , стрелы , оборудование виндсерфинга , моноласты), вёсла;
- медицинская техника;
- протезостроение
- рыболовные снасти (удилища);
- профессиональные фото- и видеоштативы;
- бытовая техника (отделка корпусов телефонов, ноутбуков , рукояти складных ножей и пр.);
- моделизм;
- струны для музыкальных инструментов;
- изготовление индивидуальных супинаторов (особенно для спорта);
- инструменты рукоделия (вязальные спицы);
- карбон слабо поглощает рентгеновское излучение, поэтому из него изготавливают окошки рентгеновских и широкодиапазонных гамма-детекторов (через которые излучение проникает в детектор).
Полимеры, усиленные углеродными нанотрубками (CNRP)
Углеродные нанотрубки , как основа углепластика в несколько раз прочнее, гибче чем резина и даже легче чем O 2 . Материал сильно отличается от обычного углеродного волокна . Такой вид углепластика применён, в частности, в конструкции самолёта Lockheed Martin F-35 Lightning II .
Примечания
- . AutoRelease.ru . Дата обращения: 15 сентября 2009. 23 августа 2011 года.
- Филиппов В. Применение композиционных материалов в авиастроении // Зарубежное военное обозрение. — 1988. — № 2 . — С. 49-50 . — ISSN .
Литература
- Справочник Дж. Любина «Композиционные материалы», М., 1988
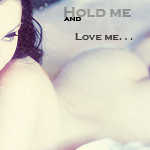
- 2021-10-11
- 1