Interested Article - Полиуретановые волокна

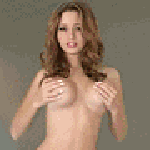
- 2021-03-17
- 1

Полиуретановые волокна или эластомерная полиуретановая нить — это синтетическая нить , получаемая на основе полиуретановых каучуков .
История
Первое промышленное производство полиуретановых нитей начато в США в 1958 году, в 1962—1964 годах полиуретановые нити появились в Европе, в 1963 году — в Японии.
Первое производство полиуретановых волокон «спандекс» в СССР было организовано в 1975 году на Волжском производственном объединении «Химволокно» по проекту всесоюзного проектного института ГИПРОИВ .
Свойства
-
Линейная плотность комплексных нитей 2,2—125 текс
- число элементарных нитей в них 3—110 и более,
- их линейная плотность 0,7—1,2 текс.
- Относительная прочность нитей 8—10 сН/текс.
- Относительное удлинение при разрыве 500—800 %.
-
Степень эластичного восстановления 95—96 %;
- модуль деформации при 300% растяжении 1,2—2,4 сН/текс.
- Влагосодержание 1,0—1,3 % (при 20 °C и относительной влажности воздуха 55—65 %);
- Плотность 1,1—1,3 г/см³; температура размягчения 175—200 °C.
У материала есть один серьёзный недостаток — он разрушается при взаимодействии с хлорированной водой бассейна или под воздействием ультрафиолета. Поэтому, например, купальник в некоторых местах становится как бы полупрозрачным и вытягивается.
Морфологическая структура

Линейные полиуретаны имеют блочную структуру макромолекул, состоящую из чередующихся жёстких и гибких сегментов с сильно изогнутыми молекулярными цепями: полиэфирных сегментов, обеспечивающих высокие эластические деформации, и жёстких сегментов, содержащих полиуретановые и карбамидные группы, обеспечивающих взаимодействие между макромолекулами и необходимую, хотя и ограниченную, теплостойкость.
Температура стеклования эластомерных полиуретановых нитей −40…−60 °C, температура плавления 160—230 °C. Чрезвычайно высокая деформативность эластомерных нитей (при невысокой прочности) позволяет использовать их в качестве вспомогательных в сочетании с обычными видами нитей, последние одновременно обеспечивают защиту эластомерных нитей от быстрого разрушения при эксплуатации изделий.
Эластомерную нить из-за химического состава часто относят к аллергенам .
Способы получения
Полиуретановые волокна производятся четырьмя способами:
- экструзией из расплава полимера;
- реакционным (химическим) формованием;
- сухим формованием из раствора;
- мокрым формованием из раствора.
Все промышленные способы получения полиуретановых волокон имеют общую стадию — синтез макродиизоцианата (форполимера) в массе из полиэфирдиола и диизоцианата (берётся в молярном избытке) при 60 °C в среде сухого азота. Последующие стадии — получение полиуретана взаимодействием макродиизоцианата с диамином (удлинитель цепи) и формование нитей проводят различными способами.
Реакцию макродиизоцианата с диамином (реакция удлинения цепи) осуществляют в среде растворителя (в основном ДМФА ). Полученный формовочный раствор дозируют через фильеру в обогреваемую (185—230 °C) и интенсивно обдуваемую горячим воздухом прядильную шахту высотой до 11 м (сухой способ) или в осадительную водную ванну при комнатной температуре (мокрый способ).
По другому способу диамин (до 3 %) добавляют в осадительную ванну с водой или органическим растворителем, в которую через фильеры выдавливают тонкими струями макродиизоцианат (или его раствор). Образование и осаждение полиуретанмочевины происходит в ванне, поэтому этот способ получения полиуретановых волокон называют реакционным или химическим формованием.
При сухом методе формования из прядильной шахты выходят 1—16 комплексных нитей, которые после нанесения замасливателя в количестве 2—7 % наматывают на бобины и подвергают термообработке в камере при 80 °C в течение 3 ч для снижения усадки нити в кипящей воде.
При мокром методе сформованные нити промывают водой (90—95 °C) в аппаратах, где они вытягиваются примерно в 1,5 раза, наматывают на бобины и подвергают термообработке при 120 °C в течение 20—30 ч. При химическом формовании нить, намотанную на шпулю, обрабатывают водой (40—80 °C, давление 4 МПа) в течение 0,25—8 ч.
Преимущества сухого способа формования перед мокрым: более высокая концентрация формовочного раствора (32 % против 20 %), большая скорость формования (600 м/мин против 150 м/мин), проще регенерация растворителя.
Развивается также способ формования полиуретановых волокон из расплава; полиуретан в этом случае должен быть термопластичным, что достигается применением в качестве удлинителя цепи диолов — этиленгликоля или бутиленгликоля.
Наибольшее распространение получил сухой способ формования полиуретановых волокон (80 % от их мирового производства), 15 % производится по мокрому и химическому способам формования, 5 % полиуретановых волокон формуют из расплава. В сухом способе для синтеза полиуретана применяют простой полиэфирдиол, получаемый полимеризацией ТГФ, в других способах — преимущественно сложные полиэфирдиолы, во всех способах — 4,4'-дифенилметандиизоцианат, иногда — смесь 2,4- и 2,6-толуилендиизоцианатов.
Ассортимент
Ассортимент полиуретановых нитей определяется их назначением. Они могут служить в качестве вспомогательных при сращивании (соединении вместе) или выпускаются в виде обмотанных другими видами нитей.
На основе эластомерных нитей в сочетании с нитями обычных видов производятся различные текстильные структуры — вторичные неоднородные кручёные и обкрученные нити с неравномерно нагруженными компонентами. Из них изготавливаются эластичные ткани и трикотаж разнообразных видов. Эластичные нити и эластичные полотна — незаменимый материал для облегающих тело текстильных изделий широкого ассортимента, в том числе трикотажных спортивных, галантерейных и медицинских.
Полиуретановые волокна известны под торговыми названиями: лайкра, вайрин (США), эспа, неолан (Япония), спанцель (Великобритания), ворин (Италия) и др.
Синонимы
- «Спандекс» (Spandex) — общее название полиуретановых эластичных нитей, которое, в отличие от названий большинства волокон, не является производным от их химического состава. Слово появилось в результате перестановки слогов в слове «expand» (растягивать). В Северной Америке предпочитают говорить «спандекс», за её пределами — «эластан» (elastane).
- «Лайкра» (Lycra) — самый известный бренд, название которого ассоциируется с эластаном. Является брендом фирмы « Invista », которая была частью компании DuPont . Особую популярность «Лайкра» обрела потому, что практически во всём мире так называли любой вид эластана. «Invista» не одобряет подобное заблуждение, всячески защищая свою торговую марку.
- Другими торговыми марками полиуретановых волокон, помимо прочих, являются «Эласпан» (Elaspan) также производства фирмы «Инвиста», «Дорластан» (Dorlastan) фирмы «Asahi Kasei» и «Линель» (Linel) компании «Fillattice».
Применение в шоу-бизнесе

- В японском сериале «Super Sentai» (в американской версии — «Power Rangers») эластан очень распространён в одежде. Впервые этот материал был использован в 1983 году в «Kagaku Sentai Dynaman» .
- В 1970-х и 1980-х годах популярность среди многих металл- и рок-групп приобрели легинсы из эластана. Основной причиной этого послужило то, что он сохранял способность растягиваться и плотно облегать тело даже после многих применений, в отличие от джинсов или кожаных штанов. Эластан не стеснял движений музыкантов на сцене, позволяя им высоко прыгать либо ставить ноги на мониторы. Легинсы из эластана носили участники Queen, Ratt, Van Halen, Mötley Crüe, Judas Priest, Scorpions, Iron Maiden, Saxon, Whitesnake, Bon Jovi, Twisted Sister и др. К концу 1980-х, когда с появлением гранжа популярность глэм-металла и металла в целом снизилась, эластан вышел из моды .
- Вместе с глэм-металлическими командами эластан носили кантри-исполнители, например Долли Партон , Марго Смит ( Margo Smith ) и Дотти Вест ( Dottie West ) .
- В фильмах « Новый Человек-Паук » и « Новый Человек-паук. Высокое напряжение » костюм паука был сделан из спандекса.
Примечания
- (недоступная ссылка)
- ↑ (недоступная ссылка)
Ссылки
- от 17 февраля 2010 на Wayback Machine
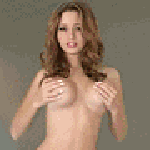
- 2021-03-17
- 1